The quality of hydraulic oil has a great influence on the working performance of the hydraulic system, and many faults originate from it. Therefore, preventing oil contamination is an important part of the use and maintenance of the hydraulic system.
The causes of impurities in the oil, the harm to the system and the preventive measures
According to relevant information, more than 70% of hydraulic device failures are caused by impurities in the oil, so care must be taken to keep the oil clean.
In order to prevent the oil from being contaminated, the pipeline must be cleaned before installation, and the components should be washed with diesel or kerosene before assembly, but it is forbidden to wipe with fabric with fibers to prevent mixing of debris.
The seal must be reliable everywhere, and it is forbidden to use seals or hoses that are not resistant to oil. The hydraulic system should preferably be cleaned in an empty cycle after the final assembly is completed.
The cause of the air in the oil, the harm to the system and the preventive measures
The main reasons why air enters the hydraulic system are:
(1) Air is directly mixed into the oil;
(2) The air dissolved in the oil is separated into the hydraulic system;
(3) Poor oil quality, poor defoaming performance, etc.
Air entering the system will cause the following main hazards:
(1) Increase the elasticity of the oil and reduce the rigidity of the hydraulic system;
(2) Because the compressibility of low-pressure air is thousands of times that of oil, even a small amount of air mixed in the system will lag the system and lose its stability;
(3) When the air mixed in the oil is compressed suddenly, it will generate local high temperature, which will evaporate and oxidize the oil, causing the oil to deteriorate and become black, and the oil is contaminated;
(4) Breaking the continuity of liquid flow, creating a "gas plug" in the small-diameter pipeline, making the valve unable to work normally;
(5) Causes irregular flow of liquid, causing blood pressure shock;
(6) After the bubbles diffuse in the oil, the lubricating performance is reduced, the chemical stability is deteriorated, and the oxidation of the oil and the rust of the parts are accelerated.
In order to prevent air from entering the oil, the following measures are recommended:
(1) Both the suction pipe and the oil return pipe must extend below the oil level and maintain sufficient depth;
(2) All parts of the system should always be kept full of oil, and a check valve can be installed at the outlet of the pump and a back pressure valve can be installed on the oil return line;
(3) Maintain good system sealing performance and replace the failed seals in time;
(4) Install an exhaust valve at the highest part of the system (usually on the hydraulic cylinder) for exhaust.
The cause of the water in the oil, the harm to the system and the preventive measures
The main reasons for the mixing of moisture are: leakage of cooling water from the tank cover; leakage of the cooler or heat exchanger, and air with high humidity intruding into the tank, etc.
The main method to prevent the oil from being mixed with water is to prevent the cooling water from entering the oil tank cover and replace the damaged water cooler and heat exchanger in time. If there is too much water, effective measures should be taken to remove the water or replace with new oil.
The damage to the system caused by high oil temperature and preventive measures
Generally, it is appropriate to keep the oil temperature of hydraulic machinery in the range of 30-50 degrees. The increase in oil temperature will reduce the viscosity of the oil, thereby increasing leakage, reducing the efficiency of the pump, and slowing down the movement speed of the actuator, which affects the stability of the work. After the viscosity is reduced, the oil becomes thinner, and the lubricating film on the relative moving surface will become thinner or even fail, resulting in increased mechanical wear. The increase in oil temperature will also accelerate the oxidation of the oil, cause the deterioration of the oil, and reduce the service life of the oil. In addition, the increase in the oil temperature will cause the valve components to heat and expand, reduce the mating interval, increase wear, and even cause the valve core to be Jamming will also cause the seal to deteriorate rapidly and lose its sealing performance.
In order to prevent the oil temperature from being too high, the following issues should generally be noted:
(1) Choose the oil viscosity correctly. Too high or low is not good for hydraulic transmission. Too high viscosity will increase the energy consumption of oil flowing. If the viscosity is too low, leakage will increase, both of which will cause the oil temperature to rise.
(2) Keep enough oil in the oil tank, choose a cooler with sufficient cooling capacity, so that the oil in the system has sufficient circulating cooling conditions.
(3) Under the condition that the hydraulic equipment is normal, the pressure of the pump should be lowered as much as possible, and the back pressure should also be lowered to reduce energy consumption and lower oil temperature.
(4) Keep the equipment clean and remove the dirt adhering to the oil tank and oil pipe in time to facilitate heat dissipation
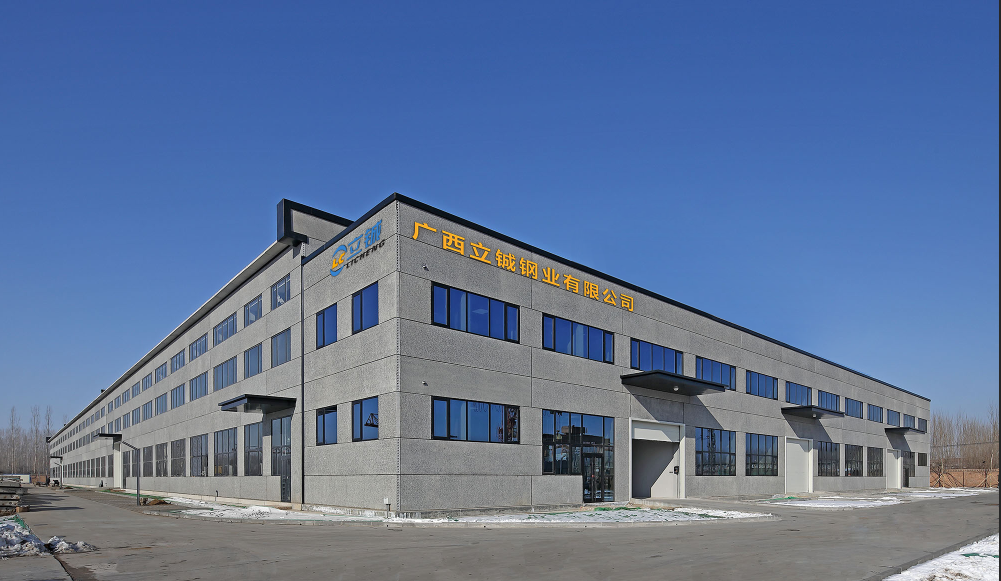